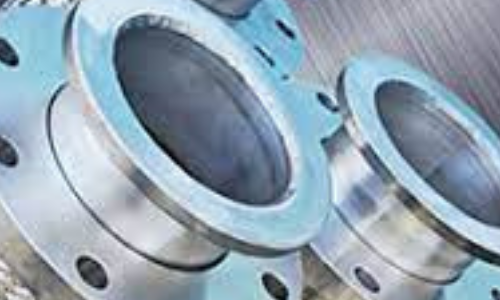
According to The Clinton Courier:
Surface treatment is the process of changing the molecular makeup of a surface so that it interacts with an adhesive ink, coating, paint, or another surface to form a strong bond. Surface treatments come in a variety of styles. Hard chrome plated layers have traditionally been used. Meanwhile, modern techniques such as laser cladding have emerged.
he key motivation for applying surface treatment is to improve protection against any corrosion or wear and tear on any part of machinery until it is finally assembled. The three-part method, which involves corona, rotor spray, and drying technology, allows for aesthetic enhancements, the correction of any flaws that might occur during the manufacturing process, and, most significantly, the system’s protection from corrosion.
Where Are the Surface Treatment Solutions?
As markets shift toward a different substrate mix based on a higher percentage of light metals, rapidly changing consumer demands, increasingly challenging quality standards, and tighter regulatory criteria for more sustainable products, successful metal surface treatment necessitates innovative products. As a result, engineering expertise at ahlbrandt provides a comprehensive range of surface treatment materials, procedures, and equipment to help you manufacture high-quality, long-lasting metal parts using highly efficient metal pretreatment processes.
Benefits of surface treatment:
- Lowered repair costs: the coatings can last longer and reduce the support costs of a vessel by up to 20%.
- Wear and tear resistance: It’s also fantastic that the amount of wear and tear your equipment endures during service.
- Corrosion prevention: One of the best things about surface treatment is how well it protects against corrosion. It helps to reduce the amount of humidity and oxygen it is exposed to, which helps to slow down the corrosion process.
- Low-friction: keeps your surfaces lubricated, avoiding wear and extending the life of your equipment.
What Is The Major Surface Treatment?
Common surface treatments can be divided into two main types:
1. Finishing and polishing
A good surface finish is desired because it increases the cosmetic appearance and the quality and protection of the pieces. A rough surface is needed for various applications, including brakes, roads, and pretreatment for painting and other coatings.
With the growing demand for precision parts with unique profiles, specified burr size and shape, and longer life, the part should be handled with technology appropriate for the end goal. The following are some of the surface treatment finishing methods:
- Thermal energy method deburring
- Electrochemical machining
- Abrasive flow machining
- Shot blasting
- Shot peening
Polishing is a crucial step in the surface preparation process. Automatic polishing will replace manual polishing in the factory, and liquid polishing wax will replace solid polishing wax due to rising labor costs and increased demand for product quality.
Furthermore, polishing is a blend of technology, practice, and artistry. It refines the surface to remove jagged edges and generate compressive residual stresses, which help to minimize wear and fatigue failure initiation. After all of the materials have been polished, the artwork is of the highest quality.
2. Coatings
Metallic coatings can be applied as a surface treatment to improve a material’s mechanical, electro-chemical, and thermal efficiency in various ways. The technique used is primarily determined by the material being used and the desired material coating or surface treatment depth.
The two most widely specified families of surface coating techniques can be classified as plating processes or vapor deposition processes, at the risk of generalizing. However, there are more sub-differences between these two distinctions:
a) Plating processes
- Hot-dipping is a continuous or batch immersion procedure in which the base alloy is immersed fully in molten zinc.
- Electroplating is an electrochemical process in which metallic ions are deposited on the surface of a bulk material via a cathodic polarization reaction.
- Cladding is a mechanical process that involves rolling or extruding two dissimilar metals together at high temperatures, resulting in a pressure-welded joint of two different metallic alloys.
b) Vapor deposition processes
- Physical vapor deposition (PVD) is a physical process that involves the movement of particles through physical material phase boundaries. It consists of applying a material surface coating through condensation of a vaporized alloy coating onto the material surface.
- In comparison to PVD, chemical vapor deposition (CVD) involves a chemical reaction between a mixture of gases and the bulk surface of the material, resulting in the chemical decomposition of some of the specific gas constituents, resulting in a solid coating on the base material’s surface.
Surface treatment has been used in industries for decades as a preventive and repair method, and it is also commonly used in computer servicing and maintenance. Your machines must still be in good working order if you want to keep production going at a profit.