
Summary: Freiborne, a seasoned chemical manufacturing company with over 40 years of experience, was sought by a prominent manufacturing firm facing safety risks and crippling operational costs due to their outdated, oil-based lubrication process in aluminum extrusion. After a thorough onsite audit, Freiborne replaced the hazardous oil-based graphite with their proprietary water-based Formlube 407 and installed a PLC-controlled application system in partnership with Fluid Transfer Systems. The results were extraordinary: near-zero smoke emissions, extended air filter lifespan, and projections of energy savings. The operation also saw an improvement in part cleanliness, which will make an expensive aqueous washer redundant in the future.
Industry: Aluminum Extruding
Category: Operational Overhaul & Process Improvement
Processes: Onsite Process Audit, PLC-Controlled Application System, Lubricant Replacement & Optimization
When a well-known manufacturing company reached out to Freiborne with an urgent need to overhaul their aluminum forming/extrusion operations, they were grappling with numerous challenges. From safety concerns and EPA air quality warnings to crippling yearly expenses for air filters, the problems were manifold. The client was using an oil-based graphite in a two-step process to lubricate the aluminum billets, resulting in acrid smoke, fires in exhaust fans, and even receiving air quality warnings from the EPA. They were also burdened with an annual $100,000 expenditure on air filters alone.
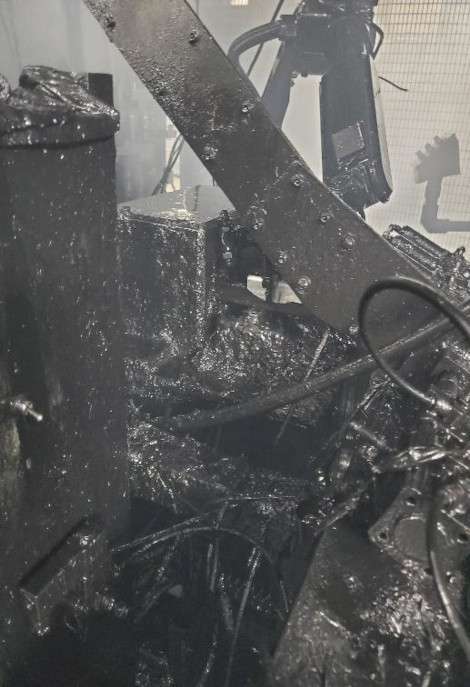

Freiborne conducted a rigorous onsite process audit, leading them to recommend their proprietary Formlube 407—a water-based lubricant specifically designed for aluminum extrusion tasks. They also suggested a partnership with Fluid Transfer Systems to create a comprehensive PLC-controlled application system for lubricant dispensing. The most challenging part was to simulate a fixed spray gun process while keeping the inductor devoid of water. After overcoming these hurdles, the optimal concentration of Formlube 407 was established.
The transformation was nothing short of remarkable. With the introduction of Formlube 407 and the PLC-controlled application system, the operation now emits almost no smoke, contributing to improved air quality and visibility within the facility. The longevity of the costly air filters increased from weeks to months. Plus, the process also saw energy savings projections due to reduced need for inductor and die heating. Most strikingly, part cleanliness improved to such an extent that the expensive aqueous washer will soon become redundant, leading to even more cost savings.
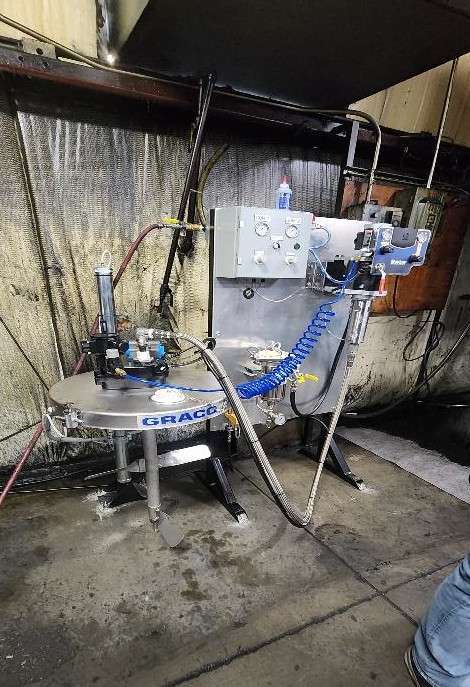
